Brief
This leading refrigeration and air-conditioning industry manufacturer encountered challenges with phosphating compressors before sending them to their paint line. The phosphate chemistry destroyed their existing unit’s doors and other components, requiring a unit with closed chambers.
Approach
The customer expressed concerns regarding the ability of a part washer to effectively phosphate their compressors as the chemistry was aggressive and would often cross into other cleaning chambers. In response, Better Engineering collaborated with the customer to conduct a successful test cleaning of the compressors at the Joppa, MD location. A custom monorail system was devised to assist the customer in addressing their cleaning challenge. Better Engineering engineered a system to complement their existing monorail system, wherein the Better Engineering monorail washer was designed to position each part into enclosed stations sequentially. Subsequently, the doors were shut, establishing a closed-system cleaning process to ensure precise chemistry management and prevent aggressive chemical reactions..
Conclusion
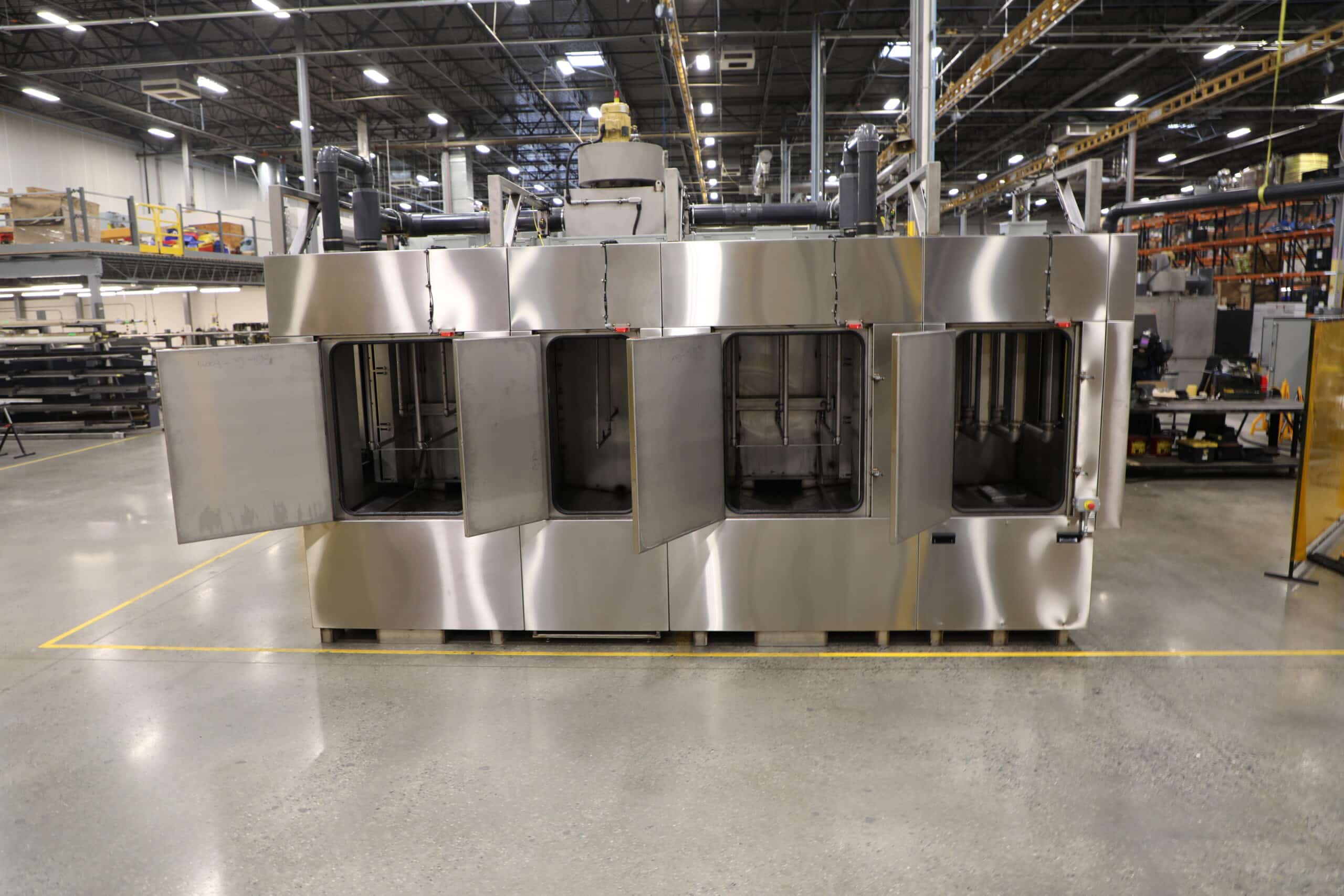
Better Engineering collaborated closely with the client to develop a customized monorail system seamlessly integrated with their existing infrastructure. The newly designed monorail washer was equipped with an automatic indexing feature for each part and incorporated a sophisticated multi-stage washing process with closed-system stages. This innovative solution was tailored to meet the client’s unique requirements and enhance operational efficiency.
Please contact us to learn about more cleaning applications and conveyor parts washers like this!