Bird flu remains a formidable challenge for the agricultural sector, posing significant threats to poultry farms and food supply chains. Implementing rigorous biosecurity measures is essential for mitigating the risks associated with this virus and other pathogens. Among the most effective agriculture hygiene solutions are high-temperature sanitizing tray washers. These systems are designed to operate at elevated temperatures, effectively eliminating pathogens and reducing the chances of contamination. The automated nature of these washers ensures consistent sanitation, thus enhancing efficiency and reliability in agricultural operations. By integrating such advanced cleaning technologies, farms and processing facilities can maintain high hygiene standards, safeguarding livestock and public health.
Understanding Pathogens in Agriculture
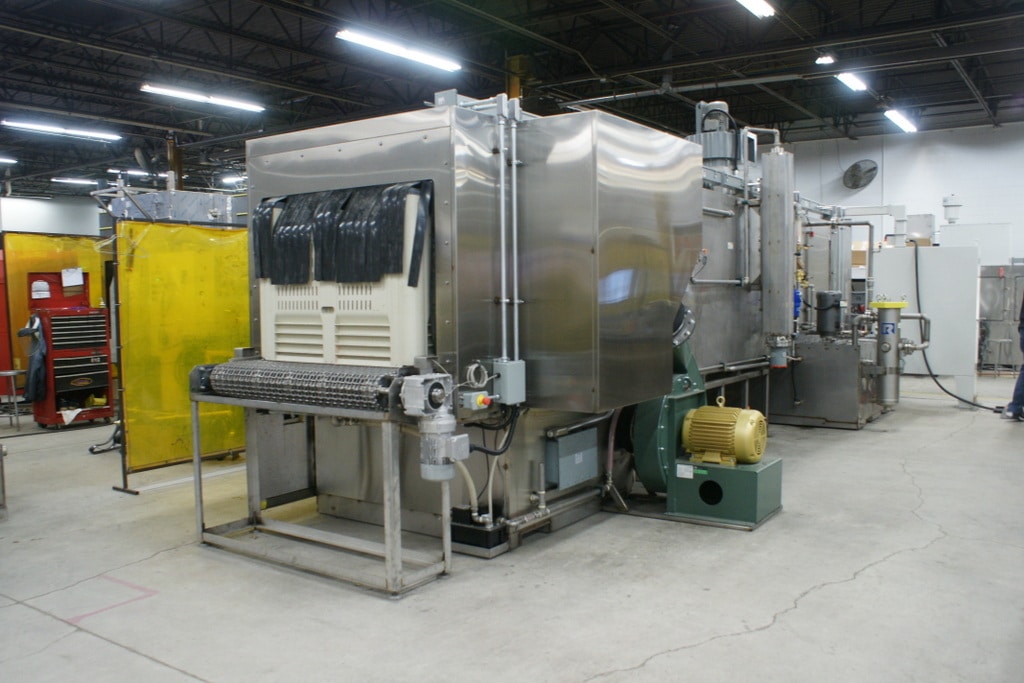
Pathogenic outbreaks present a persistent challenge in the agricultural and food processing industries, potentially disrupting production, endangering livestock, and posing risks to public health. Bacteria, viruses, and fungi can spread through contaminated equipment, including egg trays, crates, feeding tools, and processing machinery, making biosecurity measures essential. High-profile outbreaks like Highly Pathogenic Avian Influenza (HPAI) highlight the importance of proactive pathogen control, as HPAI continues to affect the U.S., causing significant economic and operational strain.
Beyond individual outbreaks, pathogens such as Salmonella, E. coli, and Listeria thrive in agricultural environments, increasing the risk of cross-contamination in live production and food processing facilities. The primary transmission pathways include contact with infected surfaces, equipment, and human handling, underscoring the need for rigorous sanitation protocols. Failure to control these pathogens can result in mass culling, product recalls, regulatory fines, and severe supply chain disruptions.
Implementing high-temperature cleaning solutions and systems such as sanitization tray washers are a proven method for pathogen control. Many bacteria and viruses, including HPAI, are neutralized at 165°F or higher, making automated sanitization systems, such as Better Engineering’s tray washers, that reach 200°F a highly effective solution. These systems ensure that contaminated surfaces do not become vectors for disease spread, reducing reliance on chemical disinfectants while maintaining compliance with food safety regulations.
A comprehensive biosecurity strategy must target all potential contamination points, from farms to processing plants. Automated, high-temperature part washers provide a consistent, sustainable, and labor-efficient method for sanitizing critical equipment. By integrating advanced cleaning technologies, agricultural operations can strengthen their pathogen defense, protect livestock, and safeguard the integrity of the food supply chain.
What is High-Temperature Cleaning for Biosecurity?
High-temperature cleaning systems are crucial for maintaining biosecurity in agricultural settings. Better Engineering’s part washers exceed this requirement, operating at up to 200°F for washing and 250°F for drying. This capability ensures the comprehensive elimination of viruses, bacteria, and other pathogens from agricultural equipment.
The automated nature of these systems guarantees consistent and thorough decontamination, reducing the chances of human error. Consistently clean results are significant in environments where meticulous hygiene is critical for preventing disease spread. Automated washers also provide the added benefit of freeing up labor resources, allowing workers to focus on other essential tasks without compromising sanitation standards.
Integrating high-temperature cleaning into biosecurity protocols ensures that all equipment, from egg trays to processing tools, is adequately sanitized. These measures help control the spread of bird flu and other diseases affecting poultry farms and food processing facilities. By maintaining high hygiene standards, these systems play a pivotal role in protecting livestock, workers, and the broader food supply chain.
Incorporating advanced high-temperature cleaning solutions into agricultural operations enhances overall safety and efficiency, making them an indispensable component of modern biosecurity measures.
What Essential Equipment Requires Precision Cleaning?
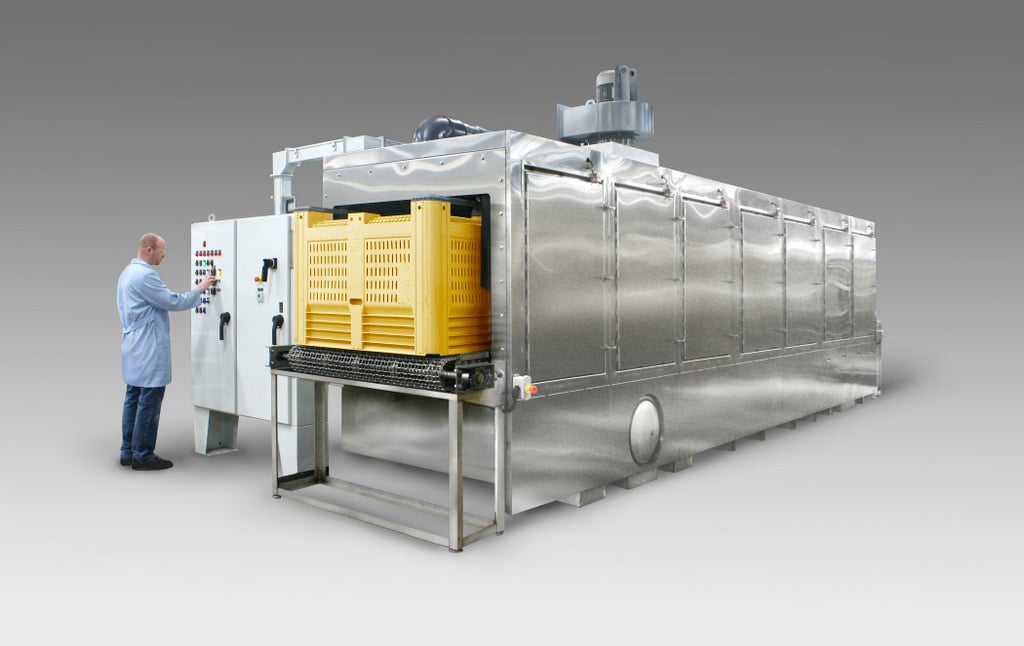
In agricultural operations, specific equipment demands meticulous cleaning to prevent cross-contamination. Egg trays and flats are critical contact points in egg handling and transport. Proper sanitization of these items eliminates virus-laden residues, helping maintain hygiene standards in hatcheries and production lines. Crates and totes, frequently used for live bird transport and food handling, can harbor pathogens if not thoroughly cleaned. Ensuring these items undergo high-temperature, automated cleaning reduces the risk of disease spread. Cages and feeding equipment directly exposed to birds also require regular cleaning to minimize contamination. Computerized systems provide consistent and thorough decontamination, crucial for maintaining the flock’s health and the safety of agricultural products.
How to Sanitize Processing Plant Tools & Containers with Automated Part Washers
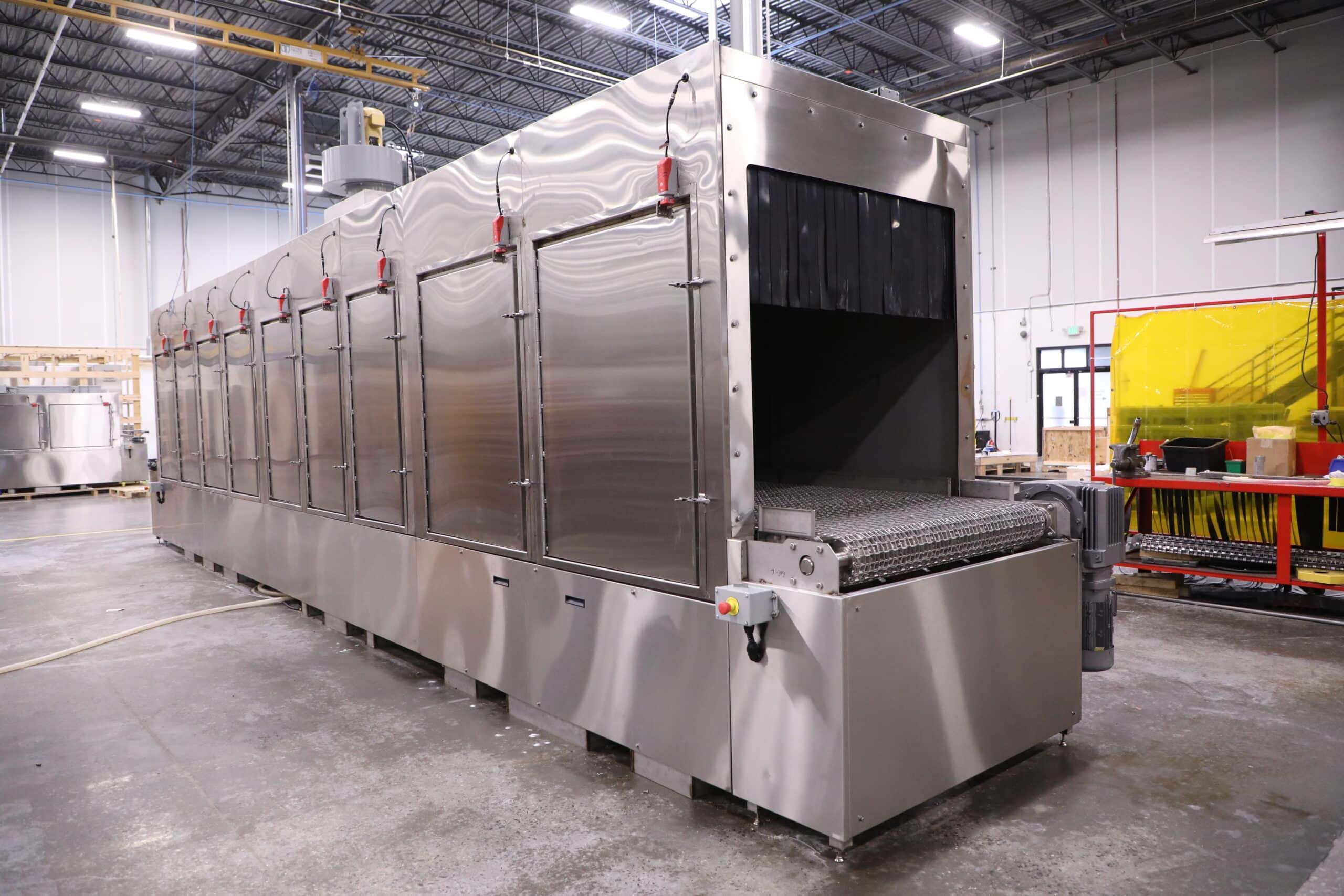
Processing plants require meticulous hygiene protocols to prevent cross-contamination, especially in tools and containers such as scalder baskets, evisceration tools, and conveyor belts. These items come into direct contact with poultry during various processing stages, making thorough sanitation crucial to maintain food safety. High-temperature sanitizing systems ensure these tools and surfaces are free from harmful pathogens.
Automated part washers can operate at temperatures that deactivate bird flu, bacteria, and other pathogens, effectively sanitizing processing equipment. This high-temperature cleaning not only eradicates contaminants but also enhances the reliability and consistency of the sanitization process by reducing the possibility of human error.
Automated sanitization tray washers and other sanitizing systems in processing plants streamline operations by providing continuous and thorough cleaning cycles, reducing downtime, and keeping the processing line moving efficiently. Additionally, automated systems can handle a high volume of equipment, ensuring that all items are sanitized to the same standard without compromising productivity.
Such advanced cleaning technologies also reduce water and detergent usage, contributing to more sustainable operations. Plants can maintain stringent hygiene standards by consistently sanitizing processing tools and containers, thereby protecting both the end product and public health. These measures are essential for controlling the spread of diseases and maintaining the integrity of the food supply chain.
What are the Benefits of Sustainable Hygiene Solutions?
Sustainable hygiene solutions, like automated part washers, offer significant advantages for agricultural operations. These washers use closed-loop systems to enhance water and detergent efficiency and recycle resources to minimize waste. High-speed drying and water reclamation features contribute to substantial energy savings, making these systems environmentally friendly. Automated handling reduces the need for human interaction with potentially contaminated equipment, thus increasing worker safety and lowering the risk of pathogen exposure.
These systems also ensure faster turnaround times, enabling continuous and efficient cleaning cycles that keep agricultural processes running smoothly. The consistency provided by automated washers means that all equipment is cleaned to the same high standard, eliminating variations that can occur with manual washing. This consistency is critical in maintaining high hygiene standards and preventing disease spread.
Incorporating automated part washers into agricultural hygiene protocols also streamlines labor efforts. Workers can focus on other essential tasks without compromising sanitation quality, improving operational efficiency. The reduced reliance on manual labor decreases the risk of human error and enhances productivity.
These advanced cleaning technologies are designed to handle a variety of equipment, from egg trays to processing tools, ensuring comprehensive sanitization across the board. By prioritizing sustainability, these solutions align with modern agricultural practices, supporting environmental and economic goals. Sustainable hygiene solutions thus play a pivotal role in safeguarding livestock, workers, and the broader food supply chain.
Better Engineering’s Cleaning solutions
Better Engineering offers high-temperature part washers, like tunnel washers, designed to meet the stringent biosecurity needs of the agriculture sector. These systems reach temperatures up to 200°F, ensuring the effective inactivation of harmful pathogens. The automated cleaning process provides consistent results, significantly reducing the risk of manual washing errors and improving overall hygiene standards.
Custom fixtures or racks can be tailored to various agricultural equipment, including egg trays, cages, and crates. This customization allows for precise and efficient cleaning, making it easier to meet industry-specific hygiene requirements. The closed-loop filtration system enhances water and detergent efficiency, minimizing waste and contributing to a more sustainable operation.
Additionally, Better Engineering’s part washers are designed with energy-saving features such as high-speed drying and water reclamation, reducing resource consumption. The automation of these systems also limits human interaction with potentially contaminated equipment, thereby enhancing worker safety and lowering the risk of pathogen exposure.
These features make Better Engineering’s part washers eco-friendly and cost-effective, aligning with modern agricultural practices. By prioritizing sustainability and operational efficiency, these cleaning solutions support environmental and economic goals, making them valuable in maintaining high biosecurity standards in farm settings.
Conclusion: Enhancing Biosecurity with Sustainable Solutions
Integrating sustainable cleaning technologies into agricultural hygiene protocols is essential for effective biosecurity. Better Engineering’s automated part washers (tunnel washers and rack washers) offer a high-temperature solution that eliminates pathogens and reduces contamination risks. Computerized systems ensure consistent and thorough decontamination, minimizing human error and enhancing operational efficiency.
Customizable features like fixturing allow for precise cleaning of various agricultural equipment, ensuring all items meet stringent agriculture hygiene standards. These washers’ closed-loop filtration and energy-saving technologies contribute to water and detergent efficiency, making the process more sustainable and eco-friendly.
Automated systems also improve worker safety by reducing direct contact with potentially contaminated equipment, lowering the risk of pathogen exposure. Faster turnaround times and continuous cleaning cycles ensure agricultural operations maintain smooth and efficient workflows.
Overall, adopting these advanced cleaning solutions supports environmental and economic goals and plays a crucial role in safeguarding livestock and public health. As the agricultural sector continues to face the challenges posed by pathogens like bird flu, investing in reliable, automated hygiene solutions becomes increasingly important for ensuring food safety and maintaining high biosecurity standards.
Interested in finding your solution? Contact Better Engineering for more information or a no obligation free parts test cleaning with data analysis.