When it comes to purchasing a part washer for your processing facility, making the informed decision is crucial. After all, this equipment will significantly impact your production line’s efficiency and smooth operation. To avoid potential issues and ensure you get the perfect washer, consider taking advantage of free part testing services offered by companies like Better Engineering. This allows you to conduct cleaning specification part testing and part washing validation testing before making a purchase. By testing with your actual parts, you can verify the chosen washer effectively meets your specific cleaning requirements.
The Relevance of Testing Part Cleanliness – Identify Contaminants with Cleanliness Testing
When you hear “cleanliness testing,” you might initially think about the aesthetics of your industrial components. However, it’s not just about the shine; it’s about the functionality, too. You can get to the heart of your component’s needs through meticulous procedures like gravimetric part testing and microscopic analysis. These tests help identify the level and nature of contaminants on your parts, allowing you to understand the cleaning process required to meet these stringent cleanliness requirements. Imagine knowing exactly what your parts need for optimal performance down to a microscopic level. Our powerful in-house microscope automatically differentiates fibers and metallic parts to a micron level.
When you decide to test wash parts before settling on a washer, you’ll get a cleaning solution that aligns perfectly with your requirements. This is the true relevance of testing part cleanliness with Better Engineering. It’s about moving beyond guesswork and assumptions to informed, data-backed decisions that can drastically improve your operational efficiency. Ultimately, it’s not just about cleanliness; it’s about excellence in all aspects of your industrial process.
Uncovering the Hidden Benefits of Part Test Washing
Part cleanliness testing offers a range of indirect advantages that could significantly impact your operations. First and foremost, it acts as a safety net, preventing expensive rework and waste associated with ineffective cleaning. This not only saves you money but also the time that would have been spent addressing issues caused by contamination.

But the benefits don’t stop there. One of the most common culprits of premature component failure is the presence of hidden contaminants. The most effective way to remove these nearly invisible enemies is through detailed part cleanliness testing, enhancing your parts’ durability.
Further, cleanliness testing can contribute to your sustainability goals. How, you ask? By identifying the specific contaminant level on your parts, you can pinpoint exactly what type of cleaning agent is required. This precision can help you reduce your reliance on harsh chemicals, thereby minimizing chemical waste. Similarly, efficient water consumption during the cleaning process can decrease wastewater generation.
Not only does this help your bottom line, but it also positions your facility as environmentally responsible. After all, in an era where sustainability is no longer a choice but a necessity, every effort counts.
Remember, cleanliness testing doesn’t just ensure your parts will pass your specifications —it also paves the way for a more efficient, sustainable, and cost-effective operation.
The Role of Test Cleaning in Preventing Facility Downtime
Every minute your processing facility isn’t running due to quality issues, which affects your bottom line. These unexpected hiccups often arise from a seemingly small oversight: inadequate parts cleaning process. Components that aren’t thoroughly cleaned can lead to a domino effect of problems downstream, culminating in significant downtime.
Fortunately, material dyne, water break, gravimetric, white glove and black light testing can help nip this issue in the bud. Here’s how:
- White Glove Testing: This meticulous visual inspection, akin to using a white glove, uncovers any visible residues or imperfections on the parts’ surface.Â
- Gravimetric Testing: This analytical method precisely measures the weight difference before and after cleaning. Any remaining residue will cause a measurable weight difference, indicating incomplete cleaning. Â
- Black Light Testing: Employing a black light helps identify any residual contaminants that might be invisible under normal light. Certain substances fluoresce under black light, making them easy to detect and eliminate.Â
- Dyne Testing: method used to measure the surface energy or wettability of a material. This is particularly important in processes like coating, painting, printing, and adhesive bonding, where the ability of a liquid to spread over a surface is critical for proper adhesion.Â
- Water Break Testing: This technique checks for the presence of oil and other hydrophobic substances that repel water. If DI water doesn’t form a uniform sheet on the part’s surface (indicating a water break), it signifies the presence of these contaminants that could hinder the cleaning process.Â
Utilizing these tests gives you a clearer picture of how well your cleaning process works. Are your parts coming out squeaky clean, or are they still harboring unseen contaminants? Testing reveals the truth, enabling you to tweak your cleaning process if necessary. As a result, the chances of your manufacturing process grinding to a halt due to dirty parts are drastically reduced. By integrating testing into your cleaning process, you’re making a strategic move to keep your operations humming along seamlessly.
Testing for part cleanliness isn’t just about ensuring your parts look clean. It’s about uncovering potential issues and mitigating risks, preventing costly downtime. Testing part cleanliness undeniably important role in maintaining operational efficiency in your processing facility.
Ensuring Regulatory Compliance Through Material Test Cleaning
In many industries, such as food processing, cleanliness isn’t just a nicety—it’s a must. Regulatory bodies are serious about upholding strict cleanliness standards and falling short can lead to hefty penalties or even an operational shutdown. So, how can you ensure you stay on the right side of the law? The answer is Better Engineering free part cleanliness testing.
Testing allows you to gauge whether your cleaning process is up to snuff. You’ll understand if your components meet the required cleanliness standards and discover any gaps that need addressing. But this isn’t just about ticking boxes for regulations—it’s about upholding the quality and reliability of your products.
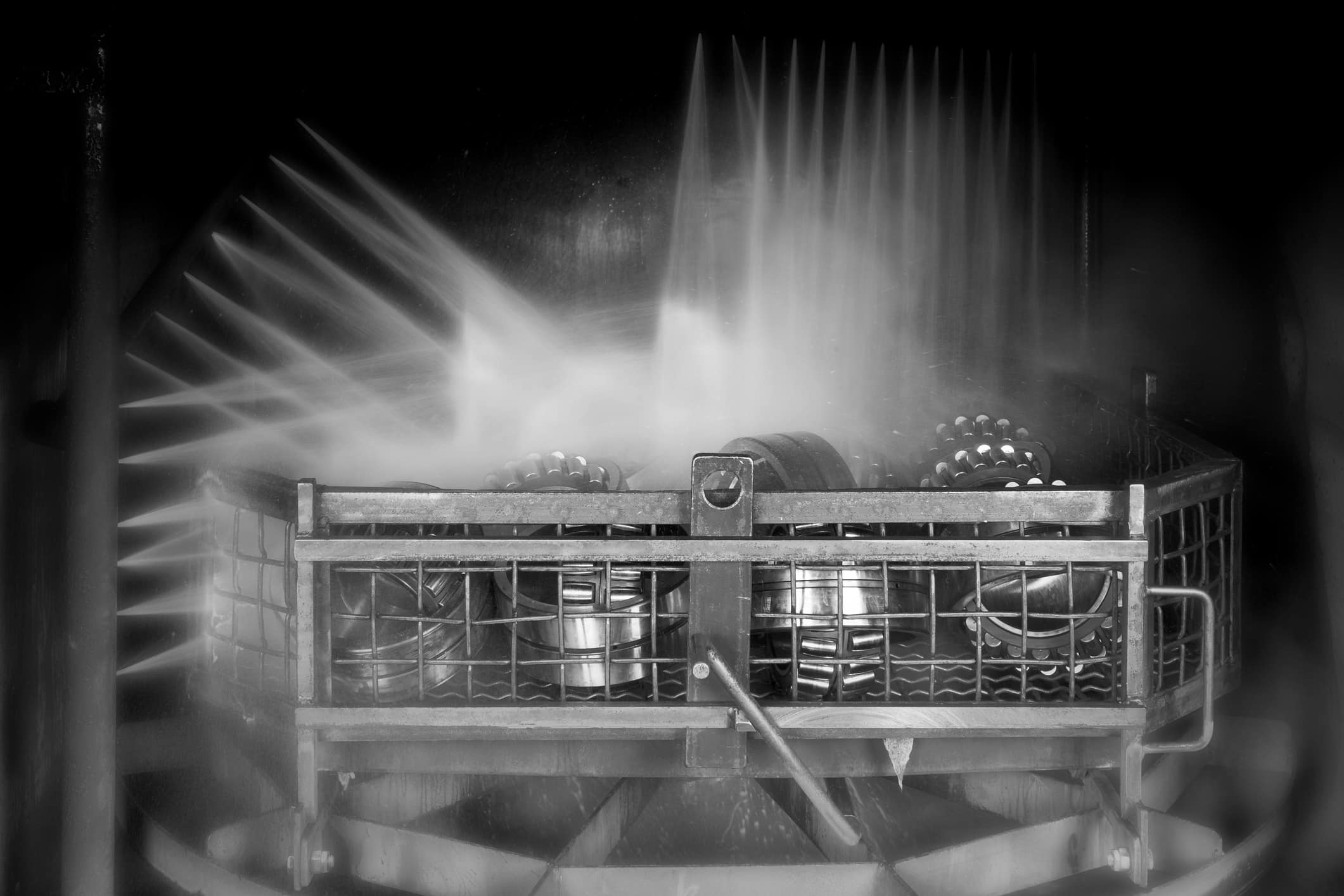
By investing in part testing, you proactively ensure your future part cleaning process is compliant. This offers peace of mind that you’re staying clear of potential regulatory hassles.
More than just maintaining your good standing with regulatory bodies, cleanliness testing prior to purchasing you washer and intermittent testing can help you build a robust reputation for reliability and quality in your industry. It’s an indispensable tool in demonstrating your commitment to excellence to regulators and your customers.
In a nutshell, free-part cleanliness testing isn’t just a smart move – it’s a vital one. It empowers you to stay ahead of potential issues, ensuring your cleaning process meets and exceeds regulatory standards prior to purchasing a Better Engineering system. With our testing, you’re making an active choice to uphold the highest standards of cleanliness in your facility, demonstrating your commitment to quality and safeguarding your operations against costly regulatory penalties downstream. After all, in the world of manufacturing, cleanliness isn’t just a virtue – it’s a vital component of success.
Customizing Your Cleaning Process Based on Test Results
The real strength of testing shines through in the actionable insights it delivers. The specific data gathered about contamination levels and types on your parts enable you to craft a cleaning process tailored precisely to your needs. Industrial component cleanliness testing is crucial in this customization process, enabling you to select the most effective cleaning system and detergents.
Imagine this scenario: your testing results reveal a high concentration of oil-based contaminants on your components. Based on this insight, you could choose a cleaning solution specially formulated to combat oil residues, ensuring a far more effective cleaning outcome than a one-size-fits-all approach. This is what makes testing so valuable; it’s a strategy for ensuring peak operational performance. The precision and personalization that testing enables, in turn, contribute to enhanced performance, increased part longevity, reduced downtime, or improved compliance. Â
So, when you take the time to test prior to your purchase, you’re not just keeping your parts clean – you’re also leveraging data to fine-tune your cleaning process. This approach ensures your components get the exact care they need, promoting optimal function and longevity. With the detailed insights testing provides, your cleaning process can become a strategic, results-driven operation tailored to your specific needs.Â
Guiding Future Investments Through Test Part Washing
Navigating the world of parts washers can seem daunting, with countless models boasting cutting-edge technology and impressive specifications. However, the right parts washer for your facility is the one that meets your unique cleaning needs, and the key to unlocking this knowledge lies in part cleanliness testing, a service we offer for free at Better Engineering.
Testing offers you a ‘try before you buy’ approach. By putting parts washers to the test with your actual parts, you can observe first-hand how effectively they clean your components. It’s one thing to be impressed by a sales presentation, but it’s another to see real results on the things that matter most – your parts.
A parts washer might have all the bells and whistles, but if it doesn’t effectively remove the specific contaminants present on your parts, it’s not the right investment for you. Parts washer test cleaning allows you to assess different washers under the specific conditions of your operation. This practical approach not only ensures you get the best value for your money, but it also safeguards your operational efficiency by preventing potential future issues related to ineffective cleaning.
Free Part Washing With Better Engineering
Here at Better Engineering, we understand that investing in a parts washer is a significant decision. It’s not just about the cost of the machine; it’s about its impact on your entire operation. Ensuring the washer is capable of delivering the cleanliness your parts require is paramount for the smooth running of your facility. Testing helps remove the guesswork from this process, guiding you towards an investment that will serve your needs effectively and efficiently.
Ultimately, parts cleanliness testing is a tool that allows you to make data-driven decisions about your cleaning process and equipment investments. We offer this service free of charge, so you can trust in the tangible results of testing your parts with different washers before you make a purchase. It’s a strategy that leads to smarter investments, ensuring the parts washer you choose will deliver the cleanliness your components demand for peak performance. After all, an investment in testing today can pave the way for a more productive and profitable future for your processing facility. To learn more about Better Engineering’s free part testing, contact us today and we’ll test clean for free.