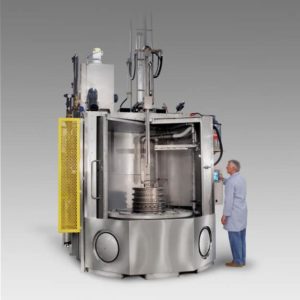
Background:
The customer is a major re-builder of jet engines. They work in conjunction with the leading international jet engine manufacturers.
Parts Cleaning Challenge:
The customer needed to replace an older parts washer that could not achieve the required cleanliness levels. The major problem was rinse water contamination. The parts held a lot of wash water which overwhelmed the small rinse tank.
Solution/System:
Twin model RD-6000-ULT systems designed for final, precision cleaning of critical jet engine components. These parts cleaning systems have a roll-in door and a spray/dry manifold that automatically lowers into the parts. Both the interior and exterior surfaces are directly impacted as the machines cycle through the following stages… wash, rinse, fresh rinse, and dry. Other features include part collision sensor for the ID manifold, all stainless steel construction, steam heat for the tanks, vacuum system, viewing window, mist collector, 10″ HMI screen, etc. Each machine features a two(2) tank system with a 60″ diameter turntable and 60″ work height.